Hemp Oil Extraction Machine
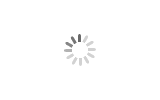
- JOSTON
- WENZHOU, CHINA
- 45 days
- 20 SETS/MONTH
we adopt the latest cold ethanol extractor technology for the hemp extractor .the extracted hemp CBD oil content is high ,less fatty and by-product content .
The content of CBD oil in all parts of hemp usually decreases according to the order of bracts, flowers, leaves, fine stems and thick stems, and the content of CBD in the flowers and leaves of female flowers is the highest, so the flowers and leaves are usually selected to extract CBD oil.
our developed hemp oil extractor machine (centrifuge machine ) is adapt the new technology can to make the extractor time short and the extractor effectivity .the extractor machine( centrifuge machine ) have the jacket which can keep the inside ethanol solution with hemp raw material in low temperature .
the main equipments of hemp extractor process line :
1). hemp grind machine : which is used to cut the hemp leaf ,stem or flower into small particle.then packed the small particle hemp raw material into small bags.
2)storage tank for the ethanol solvent : the storage tank with jacketed to cool the ethanol into low temperature ,it is usual to reach as -60 degree celius.
3)centrifuge machine :feed the grind hemp raw material into the inside chamber and add the ethanol solvent to mix together.
4) filter system : the the CBD oil & ethanol extractor solution will be filter ,the particle and the Chlorophyll color will be removed the extractor solution.
5) evaporator machine :which is used to evaporate the ethanol from the extractor solution ,which is used FFE or single effect evaporator .
6)molecular distill system : which is used to separate the CBD oil with other by-product to get high purify CBD oil products.
7)cooling system : low temperature Screw chiller to cooling the ethanol into low temperature.
8) steam system : it is used to afford the steam energy for the evaporator machine .
9) pipeline for the whole system .
10) control system :control the whole system running ,which can make as manual operation and PLC/HMI operation .
Extractor machine ( centrifuge machine ) Working steps as bellow :
1. System loading: A pre-loaded closed filter bag is placed into the basket.
2. Program Menu: The 'Spray Wash' or 'Agitation Wash' program is selected on the HMI where the RPM and cycle times are set to the operator’s specifications.
3. Fill: Alcohol is connected from source tank into the centrifuge.
4. The Wash cycle: The plant material undergoes an agitated wash with a set number of bi-directional agitations
5. System Draining: When the wash cycle is complete, the outlet valve is manually opened and theliquid drained. The alcohol wash is pumped to a properly rated storage reservoir for further processing.
6. Spin Dry Cycle: The 'Spin Dry' menu is selected on the HMI and the drying cycle is started. The wet plant solids are spun dry of the remaining alcohol mixture within.
7. System Unloading: Upon completion of the 'Dry cycle', centrifuge is unloaded by taking the filter bag out from the basket.
8. Repeat Process.
Extractor machine ( centrifuge machine ) technology data as bellow :
Specification
Type | Drum | Power (kw) | Weight (kg) | Overall size (L × W × H) (mm) | ||||
Diameter (mm) | Volume (L) | Capacity (kg) | Speed (rpm) | G-force | ||||
PPTD-10 | 300 | 5 | 10 | 2500 | 1050 | 1.1 | 180 | 890 × 600 × 500 |
PPTD-25 | 450 | 20 | 25 | 1900 | 910 | 1.5 | 250 | 980 × 650 × 870 |
PPTD-50 | 600 | 40 | 50 | 1500 | 756 | 3 | 800 | 1300 × 880 × 900 |
PPTD-135 | 800 | 100 | 135 | 1200 | 645 | 5.5 | 1300 | 1800 × 1200 × 1140 |
PPTD-135-NA | 800 | 100 | 135 | 1500 | 1008 | 7.5 | 1300 | 1800 × 1200 × 1140 |
PPTD-200 | 1000 | 150 | 200 | 1000 | 560 | 7.5 | 2000 | 2050 × 1500 × 1220 |
PPTD-200-NA | 1000 | 150 | 200 | 1200 | 706 | 11 | 2000 | 2050 × 1500 × 1220 |
PPTD-300 | 1200 | 250 | 300 | 800 | 431 | 11 | 2500 | 2350 × 1650 × 1370 |